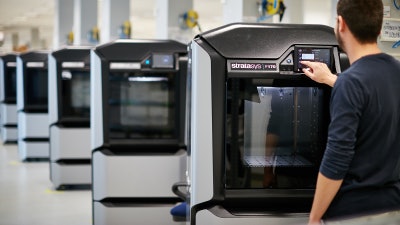
Digitalization and technology are rapidly reshaping the skillset of today's workforce. This shift underscores the immediate need for technical proficiency, digital literacy, adaptability, and critical thinking.
As industries increasingly adopt advanced technology and automation, there is an underlying expectation that workers have a deeper understanding of these technologies to remain competitive in the job market.
A recent study by the World Employment Confederation revealed that 78% of global executives are concerned about their ability to train employees quickly enough to keep pace with tech developments in the next three years. This concern emphasizes the urgent need for employers to invest in training and programs to upskill workers to ensure their workforce remains engaged and has the skills needed to thrive in a technological work environment.
Let's look at the ongoing transformation in the manufacturing industry. Today's factory floors are becoming increasingly digitized and automated with disruptive technologies like additive manufacturing (AM), artificial intelligence (AI), and machine learning (ML).
As these tools become more prominent on factory floors, workers must be digitally literate and have proficient technical skills to effectively operate and maintain new machinery. These technologies help companies bring products to market faster and make them more available. For example, AM presents opportunities to enhance production efficiencies, reduce costs, and mitigate future disruptions by enabling decentralized and distributed manufacturing. Ultimately, AM significantly alters traditional manufacturing methods, offering faster prototyping, design flexibility, shorter lead times, increased customization, and supply chain optimization.
To reap the benefits of AM, workers require skills in programming, data analysis, digital interface use, software application navigation, supply chain management, and interacting with connected devices. AM is not intended to replace traditional manufacturing methods but will complement the overall manufacturing process.
Even with the advancement of AM, there is still a considerable shortage of workers with the necessary skills to meet the demands of today's manufacturing sector. This shortage is not a future concern but an immediate challenge that requires urgent attention. According to a recent report from Deloitte and the Manufacturing Institute, the U.S. manufacturing industry is projected to face a shortage of 3.8 million jobs between 2024 and 2033, highlighting the pressing need for upskilling and training programs.
Unique opportunities exist to build a workforce skilled in today's changing industries, specifically for manufacturing employees. For example, producing anatomic models for surgical procedures in healthcare requires advanced geometries and lighter parts that traditional manufacturing methods cannot make. In racing, speed is obviously of the essence, especially in parts production.
Investing in AM reduces costs and creates efficiencies in retooling parts at every stage of the production process—in hours instead of months. Dental labs also realize these efficiencies, using AM to increase accuracy, streamline workflow, and increase lab productivity.
Lastly, organizations such as SkillsUSA support student workforce development in advancing the AM capabilities needed to scale the companies of the future. Ultimately, employers investing resources into educational opportunities and who prioritize continuous learning will be better positioned for growth.
Here are three steps that we take within manufacturing to prepare employees for today's disruptive technologies.
1) Invest in AM Training and Certification Programs
Manufacturing companies should develop comprehensive training programs covering AM fundamentals, including machine operation, software usage, computer-aided design (CAD), material selection, and automation/post-processing techniques. These skills are crucial for designing parts, preparing digital models for printing, selecting appropriate materials, and analyzing printed components. AM is just scratching the surface of its ability to integrate into the overall manufacturing cycle. Workers who learn these skills will be at the forefront of opportunities when AM takes off.
Certification programs designed for AM, such as those offered by industry associations like the Additive Manufacturing Users Group (AMUG) and the National Occupational Competency Testing Institute (NOCTI), can further validate employees' proficiency in the sector. These certifications serve as credentials for career advancement within the company and demonstrate competency to clients and partners.
2) Design Hands-On Workshops and Labs
There is no better way to learn a new technology than by working with it on the factory floor, and today, there is a trend of "3D Printing Labs" taking up residence on the factory floors of our customers. This practical experience allows workers to learn the products, materials, software, and processes to understand how 3D printing fits in with manufacturing and how it can improve the overall process. Incorporating this hands-on approach into a continuing education curriculum will equip workers with the skills to operate new, automated, and digital manufacturing systems. Providing opportunities for experimentation and problem-solving in a controlled environment will accelerate the development of the core skills needed on a digitized factory floor and help revolutionize how companies improve and expand their manufacturing.
3) Invest in Mentorship and Cross-Training Education
Cross-training and mentorship programs also enhance employee retention and engagement, foster a culture of innovation, and facilitate succession planning. Ultimately, investing in employee development ensures that manufacturing companies stay competitive in today's rapidly changing business environment.
Brent Noonan is the president of Stratasys Americas.Stratasys
The good news is by investing in continuous education, cross-training, and certifications, manufacturers can bridge this gap. Doing so ensures their workforce is digitally literate and has proficient technical skills to identify process improvements and innovation. This approach will ultimately help manufacturers stay competitive in today's global market.